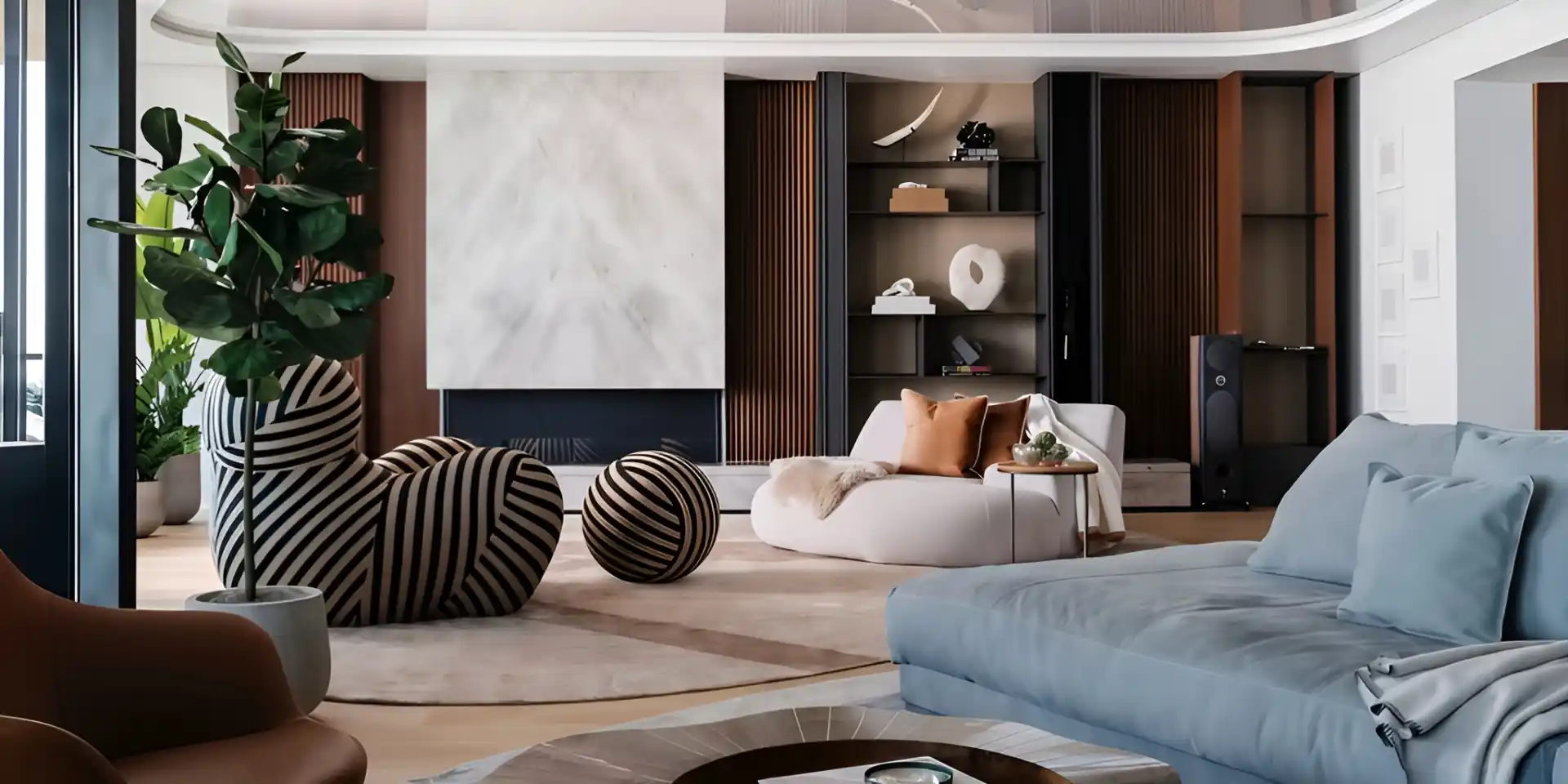
-
Project
1000 Museum Miami
Why Material Selection Matters
Material selection isn’t just a technical decision when it comes to custom cabinetry and architectural millwork, . Instead, it serves as the foundation that determines how your project will look, feel, function, and last over time.
Whether you’re designing a kitchen, closet, built-in bar, or wall paneling, each space presents unique challenges regarding humidity, structural demands, and visual expectations.
Therefore, choosing the right core material ensures that the finished product meets aesthetic goals and performs reliably in its environment.
This becomes even more important in regions like South Florida, where fluctuating humidity, salt air, and year-round use demand moisture-resistant and dimensionally stable materials.
At Lignum, we guide clients through every phase of their custom cabinetry project with a detailed cabinetry materials guide to ensure the best performance and design match.
Our team works closely with homeowners, designers, and contractors to recommend the best combination of materials based on the project’s location, purpose, and finish goals.
Understanding the differences between solid wood, plywood, MDF, melamine, and veneers helps clients make confident, informed decisions that support the longevity and success of their investment.
In this article, we’ll take a closer look at the most commonly used materials in modern custom carpentry; exploring their properties, applications, pros and cons, and how to choose the right one for your project.
Solid Wood: Beauty, Strength, and Limitations
Solid wood has long been the gold standard in custom cabinetry and millwork. It offers natural grain, warmth, and the ability to develop character over time. Many people associate it with craftsmanship, luxury, and longevity.
However, despite its undeniable aesthetic appeal, solid wood is not always the most practical choice.
High humidity, fluctuating temperatures, and demanding environments often challenge its long-term performance.
What Is Solid Wood?
Solid wood refers to boards milled directly from logs, without engineered substrates or synthetic reinforcements. Each board is unique, with natural variations in grain, knots, and color. This uniqueness contributes to its charm but also means a higher degree of unpredictability in terms of movement and finishing.
Common Hardwood Species Used in Fine Carpentry
• White Oak: Known for its strength and closed grain. Its durability makes it ideal for cabinetry, flooring, and shelving. Quarter-sawn white oak is particularly resistant to warping and has a beautiful linear grain.
• Walnut: A luxury hardwood prized for its rich, dark color and smooth grain. It finishes beautifully and adds depth to high-end millwork and furniture.
• Maple: Hard, dense, and very light in color, maple provides a clean and modern look. It’s often used for painted cabinetry and interior components.
• Cherry: A reddish-brown wood that darkens with age and exposure to light. Its fine grain makes it ideal for traditional furniture and formal millwork.
📊 Did you know? Solid hardwood can last over 50 years when properly maintained, but it also has the highest material cost per linear foot compared to engineered alternatives.
Pros of Using Solid Wood
Solid wood offers several compelling advantages that make it a preferred choice in many high-end custom projects. Its natural beauty stands out, as every board features a unique grain pattern and color variation, contributing to one-of-a-kind results in cabinetry and millwork.
In terms of longevity, solid wood can be refinished, repaired, and restored, which allows it to age gracefully and remain functional for generations.
Its structural integrity also makes it ideal for exposed joinery and heirloom-quality furniture pieces that require both strength and craftsmanship.
Furthermore, when sourced responsibly, solid wood supports environmentally conscious building practices, offering a sustainable alternative to synthetic or less durable materials.
Limitations to Consider
Despite its many strengths, solid wood also presents several limitations that are important to consider when planning a custom project.
First, cost is a significant factor, as solid wood is generally much more expensive than engineered alternatives.
Additionally, wood is a living material that naturally expands and contracts with changes in humidity. Without proper allowances in the design, this movement can lead to warping, cracking, or joint failure over time.
Inconsistent availability is another concern; high-grade lumber often varies in size, tone, and overall quality depending on the source and harvest conditions.
Lastly, solid wood is considerably heavier than its engineered counterparts, which may necessitate stronger structural supports and could restrict its use in certain vertical or suspended applications.
Where Solid Wood Makes Sense
Solid wood works best in applications where visual character and long-term durability take precedence. Craftsmen often select it for decorative face frames, floating shelving, tabletops, custom furniture, and accent elements in closets or built-ins. In humid climates like Florida, we apply solid wood sparingly and with intention.
To reduce the risks of expansion, contraction, or warping, we frequently combine solid wood elements with stable engineered cores such as plywood. This approach preserves the warmth and authenticity of natural wood while ensuring greater structural reliability over time.
Engineered Wood Explained: Core Materials in Modern Cabinetry
Although solid wood has earned lasting appreciation for its natural beauty, today’s custom cabinetry often depends on engineered wood materials. In contrast, these materials offer greater structural stability, consistency, and adaptability; qualities that meet the demands of modern living.
Moreover, manufacturers develop engineered panels specifically to minimize common issues such as warping, cracking, and irregular grain patterns. As a result, they perform exceptionally well in high-humidity regions like Florida, where environmental conditions can challenge the longevity of traditional solid wood.
Let’s explore the most commonly used engineered materials and their roles in modern millwork.
Plywood: Strength, Versatility, and Dimensional Stability
Plywood combines thin sheets (or “plies”) of wood veneer, which are glued together with alternating grain directions to enhance strength and stability. This cross-laminated construction enhances strength and reduces movement caused by changes in moisture or temperature.
Plywood plays a vital role in custom cabinetry by delivering strength, reliability, and versatility across a wide range of uses. Builders frequently use it for cabinet carcasses, shelving, wall panels, drawer boxes, and other structural components where durability is essential. Its excellent strength-to-weight ratio allows for stable yet manageable construction. Unlike MDF or particleboard, plywood holds screws more effectively and resists warping and splitting under stress or humidity.
Manufacturers offer it in hardwood-faced options like oak, maple, and walnut, which makes it suitable for both internal structures and visible applications.
Among its most trusted variants, Baltic Birch plywood provides a uniform, strong core ideal for precision work, while marine-grade plywood enhances moisture resistance in outdoor or damp spaces.
MDF (Medium-Density Fiberboard): Smooth and Stable
Manufacturers produce MDF by breaking down wood fibers and combining them with resin under high pressure to form a dense, smooth, and uniform panel. This composition makes MDF an excellent choice for precision machining and painted finishes that require a flawless surface.
Designers and builders frequently use it for painted cabinet doors, drawer fronts, detailed wall panels, moldings, and interior decorative elements where crisp edges and clean lines matter most.
Its ultra-smooth surface eliminates knots and grain irregularities, making it ideal for lacquers, paints, and even specialty coatings.
Additionally, MDF tends to cost less than plywood or hardwood, making it a budget-friendly option for visible components. However, it’s important to seal MDF properly, since its composition absorbs moisture easily. It’s also heavier than plywood and lacks the strength required for structural or load-bearing applications.
Melamine Panels: Affordable, Durable, and Easy to Maintain
Melamine panels feature a core made of either particleboard or MDF, which is laminated with a decorative melamine surface. This combination creates a durable, easy-to-clean solution that works especially well for cabinet interiors, closet systems, and modular storage furniture.
Designers often choose melamine for closet organizers, budget-conscious cabinetry, and laundry or utility room storage where practicality and cost-efficiency are essential.
These panels come in a wide variety of finishes, including textured wood grains, matte, and gloss options, allowing for considerable aesthetic flexibility.
Their surfaces resist scratches and stains, making them ideal for everyday use in busy areas. However, because the edges of the core remain exposed after cutting, installers must apply edge banding to ensure a clean and finished look.
While melamine performs well in functional spaces, it may not suit high-end, visible cabinetry unless paired with premium hardware or custom design elements.
Engineered Veneer Panels: Surface Beauty Meets Core Efficiency
Engineered veneers, such as those developed by ALPI, are thin slices of reconstituted wood bonded to MDF or plywood cores. These veneers can replicate rare wood species or create contemporary patterns with exceptional consistency.
Applications & Advantages
Veneers are especially well-suited for a variety of high-impact applications in both residential and commercial environments. They are commonly used in high-end wall paneling and cabinetry fronts, where a refined appearance and attention to detail are essential.
In commercial interiors, veneers provide the uniformity needed across large-scale installations, while also supporting creative expression in artistic millwork and branded environments.
One of their key advantages is the ability to maintain consistent color and grain patterns over expansive surfaces, which is often difficult to achieve with solid wood. Additionally, veneers offer a more sustainable alternative to exotic hardwoods, making them a responsible choice for environmentally conscious design. Their versatility extends further, as they are compatible with a wide range of finishes, from natural oils and stains to lacquers and matte coatings; allowing for complete customization based on project goals.
Veneers: The Best of Both Worlds
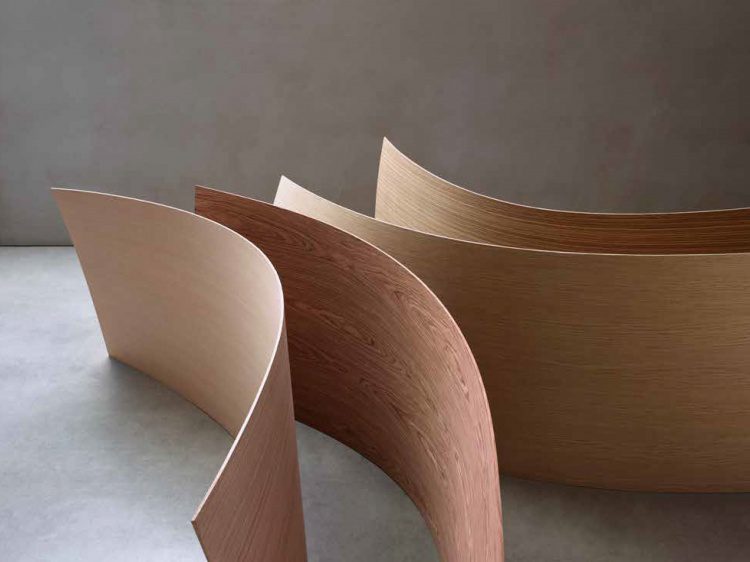
Wood veneers offer a sophisticated solution that merges the natural beauty of real wood with the performance and cost-efficiency of engineered substrates.
Veneers are thin slices of wood, typically between 0.3 mm and 0.6 mm thick, that are applied over a core material like plywood or MDF to create surfaces that look and feel like solid wood without its limitations.
Used extensively in high-end cabinetry, wall paneling, and architectural millwork, veneers allow for a more responsible use of timber resources while offering aesthetic consistency and design flexibility.
Types of Veneers Used in Custom Projects
There are several types of veneers, each suited to different visual and technical goals:
• Natural Wood Veneers: Sliced directly from logs. Each sheet is unique, showcasing authentic grain and figure. Ideal for organic, character-rich interiors.
• Reconstituted (or Engineered) Veneers: Made from fast-growing woods that are dyed, compressed, and reassembled into uniform grain patterns. These offer incredible visual consistency and are often used in commercial applications.
• Backed Veneers: Veneers bonded to a paper or fleece backing to enhance flexibility and reduce cracking during installation, especially on curved or detailed surfaces.
Advantages of Veneers
Veneers offer a combination of aesthetic flexibility and resource efficiency that makes them highly valuable in custom millwork.
They allow designers to incorporate visually striking wood species such as ebony, zebrawood, or figured maple, without relying on large volumes of solid exotic wood. This approach reduces both cost and environmental impact.
Veneers also provide consistent color and grain patterns, which proves essential in large-scale installations or matching furniture sets. Their versatility extends further, since they adhere easily to a variety of substrates like MDF and plywood, enhancing both structural reliability and design possibilities. In terms of sustainability, veneers maximize the utility of each log by yielding significantly more usable surface material per tree, helping reduce waste across the production process.
🌿 Many premium veneer brands, such as ALPI, offer FSC®-certified options and customizable grain and color combinations, bridging innovation and ecological responsibility.
Where and How Veneers Are Used
Cabinetry & Doors: Veneered panels allow for custom grain matching, book-matching, or slip-matching to create a seamless appearance across multiple doors or surfaces.
Wall Paneling: Ideal for large decorative panels where solid wood would be cost-prohibitive or unstable due to expansion and contraction.
Commercial Projects: Frequently used in hospitality, retail, and office interiors where uniformity and impact are key.
Artistic Applications: In products like our Woodxel pixelated panels, veneers are used as individual color elements, carefully selected and arranged to form unique compositions that blend design, craft, and art.
Limitations and Considerations
• Veneers must be professionally handled to avoid bubbling, cracking, or uneven adhesion. The finishing requires care to ensure the thin layer is not over-sanded or unevenly coated. Some species may be prone to fading if not properly protected from UV light.
Wood Cuts & Construction Techniques
The performance and appearance of wood in cabinetry and millwork depend not only on the material itself, but also on how it’s cut and assembled. In fact, understanding wood cuts helps explain why two pieces of the same species can look, and behave, very differently.
Additionally, the construction techniques used during the fabrication of cabinets and panels play a crucial role in determining durability, precision, and long-term stability. Therefore, selecting the right combination of cut and joinery is essential for achieving both aesthetic and structural success.
Types of Wood Cuts: How the Log is Sawn Matters
Different cuts produce different grain patterns, levels of dimensional stability, and pricing. Here are the most common types used in fine carpentry:
Plain-sawn
Plain-sawn wood, also known as flat-sawn, is the most common and cost-effective method of cutting lumber. In this technique, the log is sliced tangentially to the growth rings, which allows for maximum yield and minimal waste.
As a result, it is often the most economical option available. Visually, this cut produces the familiar cathedral or wave-like grain patterns that are especially popular in traditional and rustic designs. However, it is important to note that plain-sawn boards are less dimensionally stable compared to other cuts. They are more susceptible to cupping and warping, particularly in environments with fluctuating humidity levels, making them less ideal for certain high-precision applications.
Quarter-Sawn
Quarter-Sawn is produced by first cutting the log into quarters and then sawing each section perpendicular to the growth rings. This method yields boards with a straight, consistent grain pattern and often reveals medullary rays; visible flecks that are especially prominent in species like oak. Compared to plain-sawn lumber, quarter-sawn boards offer greater dimensional stability, making them less prone to warping and ideal for precision applications such as cabinetry, flooring, and paneling. Additionally, the clean and refined appearance of this cut makes it a favorite in both traditional and modern designs. However, the process is more labor-intensive and results in lower material yield, which leads to a higher cost overall.
Rift-Sawn
Rift-Sawn are cut at a consistent angle, typically between 30 and 60 degrees, to the growth rings of the log. This method produces an exceptionally straight and uniform grain pattern without the flecking seen in quarter-sawn cuts. As a result, rift-sawn lumber is highly sought after for modern, clean-line designs where symmetry and subtle texture are key. In terms of performance, it offers excellent dimensional stability, making it ideal for high-precision applications such as vertical grain cabinetry, custom furniture, and millwork in humid environments.
However, due to its cutting technique, rift-sawing generates significant waste and has a very low material yield, which makes it the most expensive option among traditional lumber cuts.
🪵 At Lignum, we often recommend quarter- or rift-sawn white oak for high-end cabinetry and wall panels where stability and consistency are paramount.
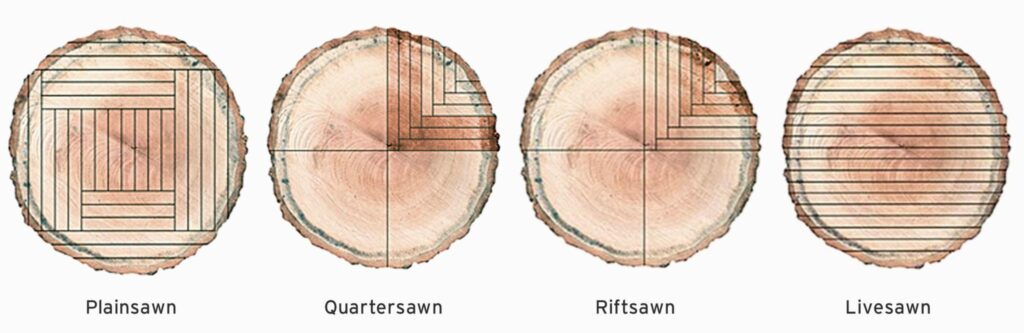
Joinery & Assembly: Craftsmanship Beneath the Surface
While hidden from the finished product, construction techniques play a critical role in strength, function, and longevity. Some of the most reliable methods include:
Dowels
• Wooden or metal pins inserted into aligned holes for added strength.
• Common in drawer boxes and carcass assembly.
Dovetail Joints
• Interlocking “tails” and “pins” used in high-end drawer construction.
• Strong, durable, and beautiful—even when left exposed.
Mortise and Tenon
• Traditional method where a “tenon” (tongue) fits into a matching “mortise” (slot).
• Often used in frame construction and larger structural joints.
Biscuits and Dominos
• Small oval or rectangular inserts glued into slots to align panels.
• Efficient for panel gluing and large surface connections.
Mitered Joints with Reinforcement
• Used for clean, seamless corners in modern cabinetry.
• Reinforced internally with splines, dowels, or lamellos.

Why It Matters
Understanding how wood is cut and assembled is more than a technical detail. It directly impacts the final outcome of any cabinetry or millwork project.
The grain orientation influences how a surface looks and how it reflects light, which affects the overall tone and visual consistency of the design.
In addition to appearance, stability plays a critical role; selecting the appropriate cut and joinery method helps minimize common issues like warping, cracking, or misalignment, especially in areas with fluctuating humidity.
Finally, the level of craftsmanship involved in joinery significantly determines how well a piece performs over time. Kitchens, closets, and commercial interiors all demand structures that can withstand daily use, making precision joinery essential for both function and longevity.
Choosing the Right Material for your Custom Cabinetry
No single material is universally superior. It all depends on the specific application, environment, design intent, and budget. At Lignum, we guide our clients through this decision-making process by balancing performance, aesthetics, and long-term value.
Below is a breakdown of how we typically match materials to project types, based on years of experience working across residential and commercial environments:
Custom Kitchens
Selecting the right combination of materials is essential to ensure both durability and visual appeal; especially in high-humidity environments like Florida. Builders typically rely on plywood for the cabinet boxes, as it offers superior moisture resistance and structural strength.
For cabinet doors and elements requiring a flawless finish, MDF or engineered veneer panels provide an ideal surface for paint or lacquer, while also maintaining dimensional stability. When it comes to cabinet interiors, particularly in base cabinets or utility areas, melamine presents a practical and budget-conscious choice.
Its easy-to-clean surface and resistance to scratches and stains make it perfect for daily use without sacrificing functionality.
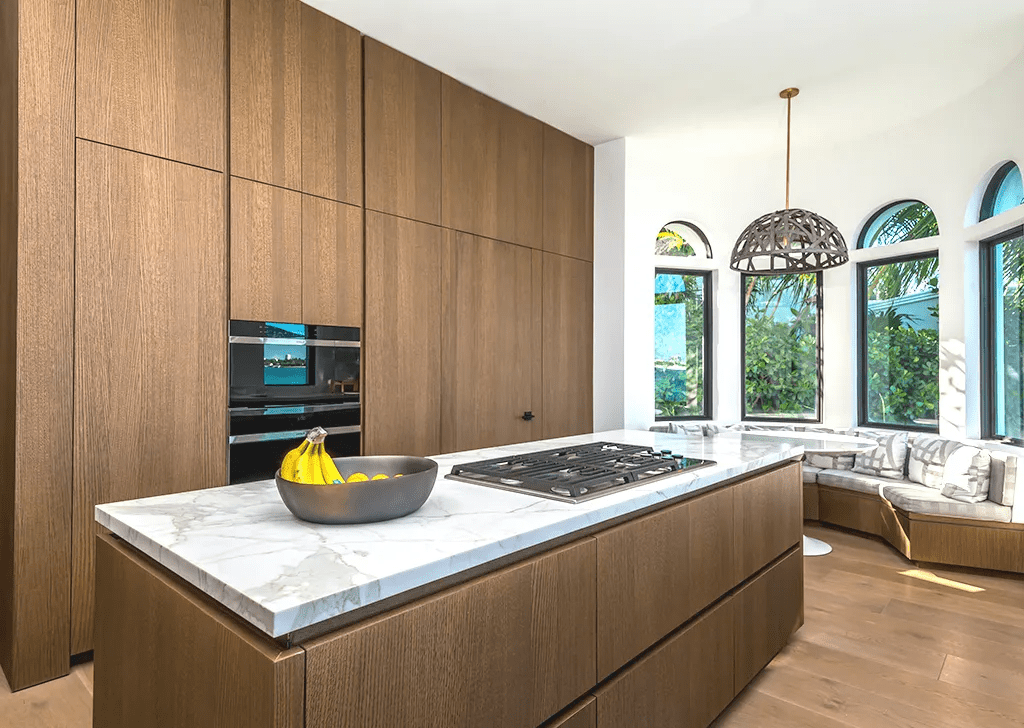
Closets and Wardrobes
Custom closets and wardrobe systems require materials that balance practicality with refined design. For the interior compartments, melamine stands out as a smart solution thanks to its cleanable surface, durability, and cost-effectiveness, making it ideal for everyday storage needs.
For the structural framework and drawer components, fabricators often turn to plywood or MDF, depending on the desired strength and finishing technique.
To elevate the overall appearance, veneers offer an elegant option for closet doors and decorative panels, delivering the look of high-end wood without the weight or movement of solid lumber.
This combination allows for easy maintenance inside the closet, while the exterior showcases craftsmanship and sophistication.
Built-In Bars & Wine Storage
Built-in bars and wine storage units serve both a functional and aesthetic purpose, often becoming focal points in entertainment-oriented interiors. To achieve durability and visual sophistication, fabricators commonly use plywood or veneered MDF for the exposed cabinetry.
These materials provide structural reliability while offering a refined appearance when paired with premium finishes. For a luxurious and consistent grain pattern, engineered veneers add a high-end touch that reinforces the overall design statement.
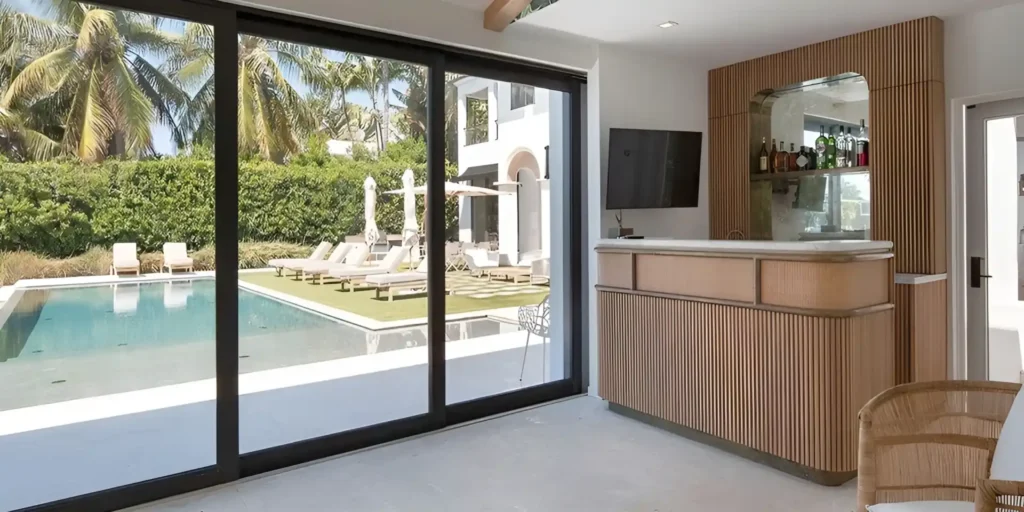
In hidden or utilitarian areas, such as back panels and utility drawers, melamine remains a practical choice thanks to its cleanability and resistance to wear.
This thoughtful material combination ensures that both the visible and functional elements of the bar work seamlessly together.
Wall Paneling & Decorative Accents
Wall paneling and decorative accents require precise material choices to ensure visual consistency, dimensional stability, and long-term performance; particularly when working with large vertical surfaces or intricate geometric patterns.
For high-end feature walls, many designers prefer rift- or quarter-sawn solid wood, as these cuts offer superior flatness and a refined, linear grain that elevates the overall aesthetic.
In both commercial and residential applications that demand uniformity and scale, veneered panels provide a practical solution by combining the look of natural wood with engineered reliability.
Depending on the selected finish and the desired level of durability, MDF or plywood cores serve as stable foundations that support a variety of styles and applications.
Commercial Millwork
Commercial millwork demands materials that can deliver consistency, scalability, and durability under frequent use.
To meet these requirements, fabricators often turn to engineered veneers and laminated panels, which provide clean, repeatable finishes across large areas; ideal for offices, retail spaces, hospitality settings, and other commercial environments.
For hidden structural elements or interior compartments, melamine offers a practical and cost-effective choice due to its resistance to stains, scratches, and daily wear. When a project involves heavy-duty use or large panel spans, plywood adds the necessary structural support while maintaining dimensional stability. Together, these materials create efficient solutions that balance design integrity with real-world performance in high-traffic spaces.
Pro Tip
When selecting materials for any custom millwork project, asking the right questions can clarify which options will deliver both function and longevity.
Start by considering whether the surface will be visible or structural, and whether it will be exposed to moisture or temperature fluctuations.
It’s also important to weigh the priorities between ease of maintenance and consistency in finish. These simple yet strategic questions help identify the ideal combination of core materials and finishes; ensuring that the final result not only aligns with your design goals, but also performs reliably over time.
Sustainability & Sourcing: Responsible Material Use
Today’s design decisions carry more weight than ever; not only in aesthetics and functionality but also in their environmental impact. At Lignum, we believe that building beautifully should never come at the expense of the planet. That’s why we carefully consider the origin, composition, and lifecycle of every material we use.
Why Sustainability in Millwork Matters
• Deforestation and Waste Reduction: Choosing responsibly sourced wood and engineered products helps reduce unnecessary depletion of forest resources.
• Air Quality & VOCs: Low-emission materials contribute to healthier indoor environments, especially important in residential applications.
• Consumer Expectations: Modern clients are more likely to choose brands and contractors who align with sustainable values.
🌿 According to a 2022 Houzz survey, over 70% of homeowners said they would consider eco-friendly materials and practices as part of their renovation decisions.
Material Choices that Support Sustainability
Choosing sustainable materials is not only a responsible design decision but also a practical one. Engineered wood products such as MDF, plywood, and veneers make more efficient use of harvested timber by producing a greater surface yield per log, which significantly reduces overall waste.
Melamine panels, although synthetic, often use recycled cores and can be sourced locally, helping to lower transportation emissions and minimize the project’s carbon footprint. For finishes that replicate the beauty of rare woods without contributing to deforestation, reconstituted veneers, like those produced by ALPI, offer an eco-conscious alternative.
These veneers rely on fast-growing species and advanced manufacturing techniques to emulate the look of exotic hardwoods, all while preserving at-risk forest ecosystems.
How Lignum Practices Sustainability
At Lignum, we take sustainability seriously by integrating responsible practices throughout our material sourcing and fabrication processes.
We collaborate with trusted suppliers who offer full traceability for their wood and composite products, ensuring transparency from forest to finish. In every project, we recommend engineered solutions, such as veneered panels, MDF, and plywood, that strike a careful balance between performance, appearance, and environmental responsibility.
Additionally, we strive to minimize waste by using precision CNC cutting technologies and repurposing offcuts whenever feasible. We are also proud to partner with forward-thinking brands like ALPI, recognized for producing FSC®-certified, low-impact wood veneers through innovative and sustainable manufacturing techniques.
Conclusion & Professional Recommendations
Choosing the right material is one of the most important decisions in any custom millwork or cabinetry project. It influences everything from how your project will look and perform, to how well it ages over time, to the sustainability of your home or business space.
In this article, we explored the essential materials and techniques that define high-quality custom cabinetry and millwork.
We examined the timeless character and strength of solid woods, alongside the stability and versatility offered by engineered products like plywood, MDF, and melamine.
We discussed how veneers merge beauty with efficiency, allowing for consistent aesthetics and resource-conscious design.
Additionally, we highlighted the importance of cutting and joinery techniques, which directly influence both durability and visual precision.
Finally, we emphasized the value of sustainable practices, which align exceptional craftsmanship with environmental responsibility.
At Lignum, we don’t just build beautiful pieces. We guide our clients through material choices that align with their vision, budget, and environment. Whether you’re planning a custom kitchen, a built-in bar, elegant wall paneling, or a full architectural millwork package, understanding your material options is the first step to a successful result. Our approach to high-end custom millwork is rooted in knowledge, precision, and long-lasting material selection.